This article is sponsored by Air dynamics industrial system corporationA company that specializes in industrial air and material solutions.
In his report on combustible dust in 2023, Dust Safety Science found that there were 263 fires and 53 explosions worldwide in connection with flammable dust from January 1, 2023. Incidents like this led to 94 injuries and 62 deaths.
A small company in Veteran ownership in York, Pennsylvania, deals with the challenges of air and particle control to prevent such disasters. Since 1991, the Air Dynamics Industrial Systems Corporation has developed standard and customer-specific products such as industrial vacuum systems, ventilation systems, pneumatic conveying systems and more for industries that range from food and drink to aviation and space and difficult production.
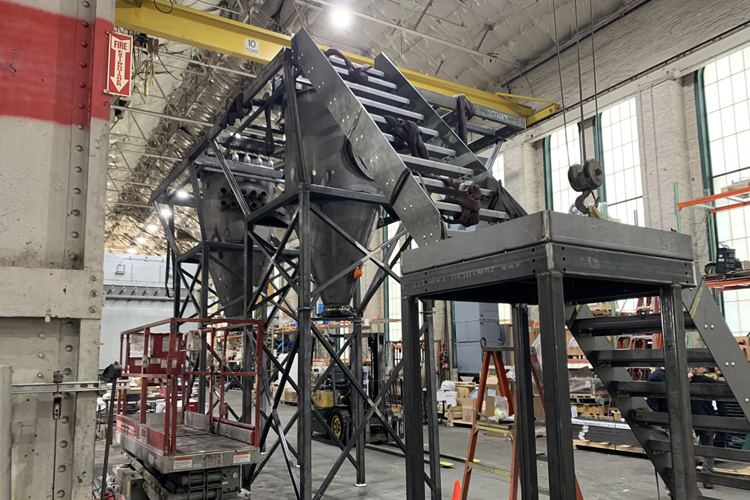
“We are a small but powerful company. Air Dynamics has the tools that are required for a customer with a process of process quality or a risk for an investment explosion,” explains Daniel Lehman, President and founder of the company. “We concentrate specifically on the safety of staff through air and particle control as well as on the preservation of assets through security systems.”
The company's products that can keep standards like Osha and Mil-Spec are developed and built in the USA. The Air Dynamics team provides “scientifically controlled solutions at the company level” with products with products that are developed and manufactured on order.
Thomas Insights (Ti): Would you share something over your background as a company founder?
Daniel Lehman (DL): I am a lifelong learner when it comes to all mechanical things. I grew up on a small farm and was exposed to machines to grow plants and raise animals. Everything had a process and often included problem solutions. I also took part in a program for industrial skills in the local school in grades 7 to 12.
After graduation, I entered the US air weapon and landed a position in aircraft navigation systems. I was responsible for the computer-aided maintenance of the Lockheed C-5 Galaxy. After the military, I was a field service engineer who installed hardware and software on various computer types. That and my military service familiarized me with the computer systems that I would later use for air dynamics.
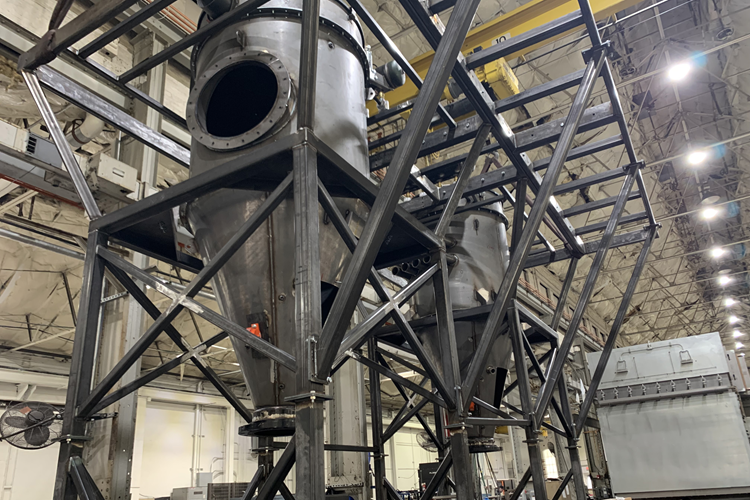
Ti: How did Air Dynamics started her start?
DL: While I had jobs in the job Commercial Computing Systems, I started a part -time business in which I installed central vacuum systems. I had seen an episode of Bob Vilas Show “This Old House” with these systems. After I contacted the local dealer, ordered and installed one, I was impressed by their efficiency.
This business went full -time in the early 1990s. One day I received a call from Harley Davidson. They wanted an industrial vacuum system, so I went to the library and saw the Thomas Register of the American manufacturers on the shelf. I found an industrial vacuum company, bought the necessary equipment and with the help of friends and my father at the weekend I installed it. This project ended my work on residential systems.
Learning and building on this basis, my experiences and exposure to problem solutions transferred to what the air dynamics do now. The C-5 galaxy had a malfunction analysis and recording system or a number of sensors. They returned to a computer system so that the flight engineer could determine in real time if something is wrong. This is similar to our current air and particle control systems.
An instrument that is located on system parts reports the operating parameters for a central processor. We can either display this information on the “Human Machine interface” screen or from a distance. If a customer has a problem, we contact him to close a cable into its system and put on halfway around the world if necessary to remedy or help with the necessary software changes.
Ti: What about Air Dynamics' approach for projects that the company distinguishes in your industry?
DL: We are ready and able to take full responsibility for all aspects of a project, from design and manufacture to device setup and on-site acceptance tests. If the customer does not know how to solve a problem, we will create a concept for him. We will sit down with you to understand the challenges you have and collect location data before we put the system into operation.
We determine the required air flow, the hose diameter and the length etc. I think we have almost 400 different controls and calculations that we carry out for a typical system. After we have been identified all system parameters and have been temporarily and finally designed, we start building the machines.
We have a 23,000 square meter system, which is fully equipped with plate bending and roller machines, welding and coating equipment and 3-phase overhead cranes. The room is crucial for the production and testing of devices in the house on the scale that we manage. For example, in three parts we built a 43 -foot dust collector with a section of 19,000 pounds.
As soon as the devices are installed, Air Dynamics offers all documentation for mechanical-electric drawings and operating manuals for end users. We will also train operators if necessary. We work seamlessly with maintenance and security teams, furnishing engineers and stakeholders to integrate the equipment into your facility.
Military and DOD projects require factory acceptance tests. We will set up the machine in our facility, operate it and then operate for a test period. As soon as the system has passed, we switch to dismantling and send it to the construction site. By being responsible for the design, we keep control of project quality and delivery. The customer can even come in the way and see progress.
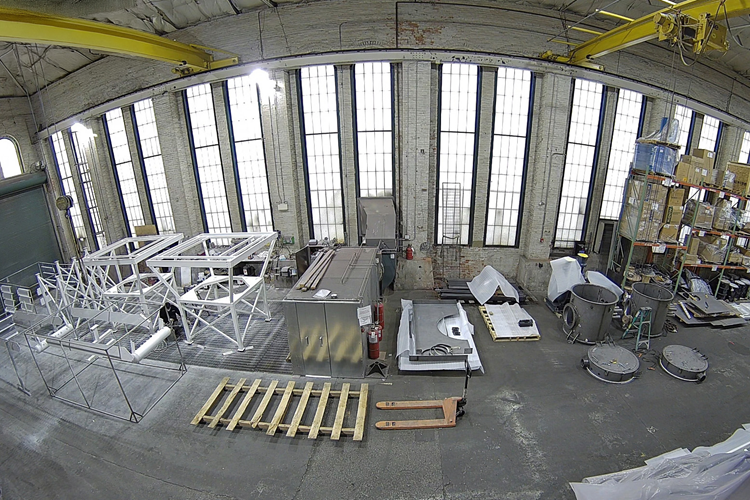
Ti: What is an example of a time when you have helped a customer to overcome a system or process challenge?
DL: Every time people fly there is an inherent risk. The safety of the flight has been supporting the aerospace industry since 2006. One of our Aerospace Manufacturing customers has around 16 of our systems that are installed between 2006 and last December. We have equipped 1 million square foot of your facility. The systems we installed also had over 1 million hours in operation without downtime.
At first we started that the customer had no longer worked from the start. They agreed that these systems were too cumbersome with three or four different designs to maintain them. We have summarized the systems in a single design so that the customer, as soon as he was trained on a system, could all maintain them.
Their industrial vacuum system is designed in such a way that people can build aircraft to remove foreign bodies while drilling, assembling and using the craft together. The worst thing that can happen when you are in the air is that a remaining mother or a bolt can slip out of the manufacturing process when the craft turns and the flight control dies. Since this system is critical, the manufacturer cannot move the production line unless all vacuum systems are in operation.
Ti: Do you see any trends in your industry in relation to security concerns? If so, how does the air dynamics address you?
DL: The continued trend I see is the ability of man to adapt to their working conditions without being aware of the dangers in their environment. My father was asbestos applicator. I have a picture that he cuts an asbestos with a measuring helmet and safety glasses, but nothing for protecting the airways. It made me sensitive to exposure to dangerous material for the staff.
In 2008 Georgia's imperial sugar plant blew into the air and 16 people. Osha admitted 33,000 manufacturers in the entire US dealings with flammable dust. This can be grains, organic materials and plastic or metal dust. There are some dangers in the production of US goods for each industry.
Every time it is a little dangerous – flammable or chemical dust – the air dynamics pursue a very conservative approach. Our systems were tested by industrial hygienists and always exist. The performance of our air material separators is of the greatest importance.
To learn more about air and material-moving solutions, contact Air dynamics Today.