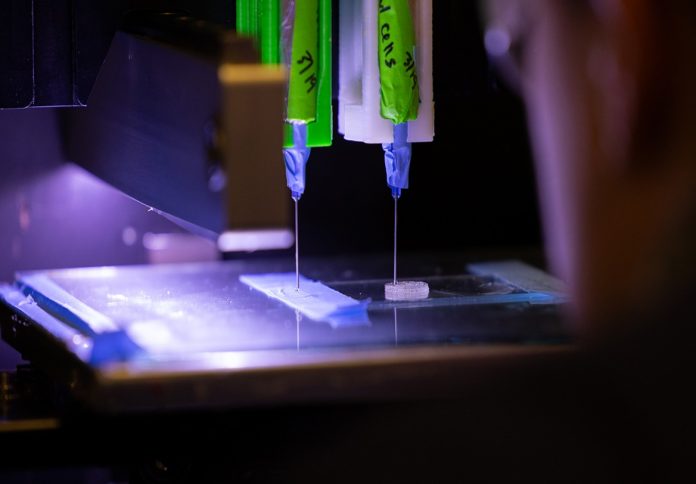
A research group at the University of Washington creates innovative 3D printed materials that are designed for use in areas such as medicine, engineering and construction and focus strongly on ecological sustainability.
Under the direction of Alshakim Nelson, Professor of Chemistry and Fellow of the Nist Faculty, the team focuses on the innovation of the materials used in 3D printing, and not the hardware or software.
The group has created a number of biodegradable and mechanically robust materials and often formulated them from the ground up if commercial options have proven to be inadequate as inadequate as a university said in a press release.
“We needed a material that was 3D -printable and biodegradable, but also had good mechanical properties,” said Nelson. “It had to be competitive with the commercial plastics that are out there today.”
Nelson, who entered the UW College of Arts & Sciences in 2015 after a decade of IBM, works in the disciplines in relation to disciplines and works with researchers from the UWS Colleges of Engineering and Medicine, the University of Texas in Austin and Mount Sinai in New York. His 18-member laboratory includes students and doctoral students as well as postdoctoralands.
Her innovations include a biolor that becomes stronger when the stress has been exercised. The team found that a specially developed grid structure enables the material to recover from the deformation and increase stiffness – a finding that the students in Nelson's laboratory first observed.
The grid structure developed with Lucas Meza, a mechanical engineering professor on the UW, helps to distribute energy under stress, which reduces the risk of cracking.
“I have a really great team of students and postdocs that make excellent observations,” said Nelson.
“You are just good scientists and notice when something interesting happens and should be examined more.”
The research of the group also includes 3D printed materials that are embedded with microorganisms that can produce therapeutic connections.
These materials can remain stable in a dried state for up to six months and become active in a suitable medium.
“You can continuously establish the desired connections for one year or more,” said Nelson.
“The big dream is to consider it for the production on a local scale and possibly in smaller volumes as required.”
With a view to the future, Nelson sees potential applications outside of earth. He said NASA could use the technology for missions that require long-term care with medication such as penicillin or antitumor active ingredients to enable on-demand bi-production in space.
“If you think of a mission to Mars that lasts almost two years, you have to take everything with you,” said Nelson.
“Could we use this type of printable structures for the on-demand production of various therapeutic connections? I think that is possible.”
The team closer to home and also researches vegetable protein sources for its 3D printing materials such as genetically modified rice.
Nelson said this development could offer a more sustainable alternative to animal proteins and expand the functionality of printed materials.
“It is just another opportunity for us to use our ideas about what is now possible – and what comes next,” he said.