Japan is known for his lightning -fast ball trains. Now it can also be a global pioneer in the ultra -fast station building. In a groundbreaking project, the workers replaced a 75-year-old shelter in rural areas with a completely 3D-printed structural structure in less than six hours.
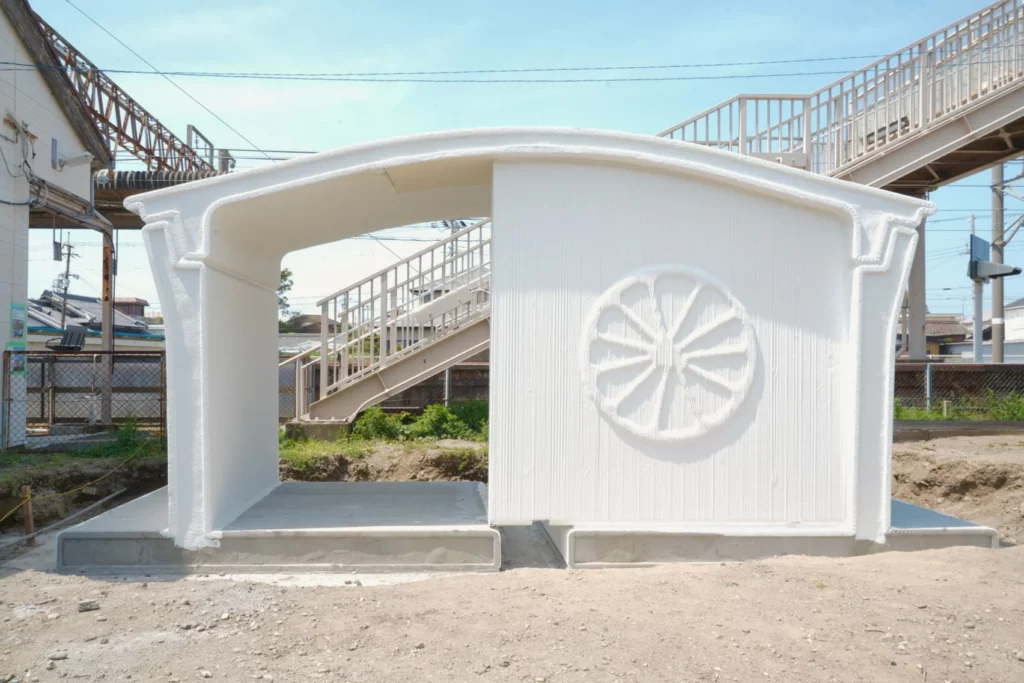
Hikyō stations
The structure at Hatsushima station is located in the coastal town of Arida, Prefecture Wakayama, and is now the first 3D-printed station building in the world. The structure is compact, weatherproof, earthquake resistant and mostly made outside of the location with a digital printer. It is not the largest station that you will ever see, but it's robust and robust.
It was built by West Japan Railway Company (JR West) in cooperation with an architectural studio called Neuob and Serendix, a startup known for the construction of affordable 3D printed houses.
The maintenance of rural, unused train stations in Japan has been a challenging task for years. You even have a name for you: Hikyō station.
A Hikyō station is a remote, often unused train station in rural Japan, which is usually far away from large cities or cities and is known for its picturesque or nostalgic attraction. These stations are important in this context, since their low passenger numbers and isolated locations make it ideal candidates for inexpensive, fast 3D printed upgrades.
But that is easier said than done.
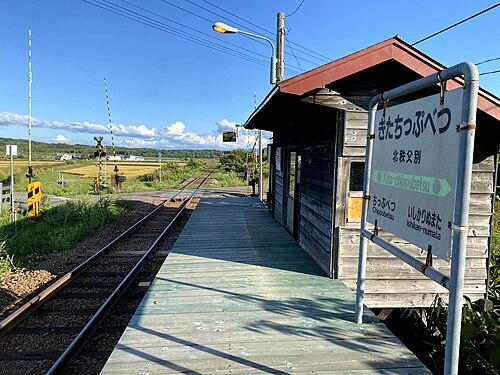
The population groups in such areas agree, the construction workers are less and many remote stations see only a handful of daily commuters. The structure or renovation of such stations requires a lot of money, months and heavy workers. With the 3D printing, however, all of this could change.
“As a rule, the construction of a station of the same size using reinforced concrete would take one to two months. In addition, there is a remarkable lack of workers in the construction industry in Japan, which leads to increasing labor costs and difficulties in securing building staff” This.
“While the 3D-printed station consists of robust and durable concrete, the structure of the structure was made possible in just two hours of the speed of just two hours and numerous station constructions,” added the serendix team.
The emergence of the 3D printed station
The process began in a factory in the Kumamoto prefecture, in which the components of the station were printed using a mortar reinforced with steel amplifier. The pressure phase lasted about seven days. After completion, the parts were loaded onto trucks and over 500 miles (~ 800 km) was transported to the train station.
The meeting occurred overnight during the gap between the last train of the night and the first of the morning. After the last train teared off at 11:57 p.m., a team of workers used cranes to put the four prefabricated parts together, and this process took two hours.
Next, the workers anchored the segments by inserting metal poles into designated slots and applying adhesive to stick to the entire structure. You completed the basic structure the next day until 5:45 a.m. The entire process took less than six hours, a dramatic improvement compared to conventional methods that lasted several weeks and would have cost at least twice as much.
The compact white building is about 2.6 meters high and covers a little more than 100 square foot. It also contains artistic reliefs by Mandarin -Orangen and Various, which are symbols of local Japanese culture.
“In order to reflect the local properties, we have expressed the local specialties, mandarin -oranges and Cutlassfischen to relief, which is another feature that is clearly possible with 3D printing.” Hiroshi Ota, founder of Neuob, told This.
While the main structure is complete, the final work, such as the installation of ticket machines and digital readers, will probably end until July when the station begins with the functionality.
A blessing to expire the public infrastructure
This project could have a major impact beyond a city. For example, in aging countries such as Japan, South Korea or Poland, in which the rural infrastructure is decades, it is expensive and urgently needed, the 3D pressure approach as a groundbreaking approach for the reconstruction of infrastructures.
Since more and more population migrates to cities (both in developed and in developing countries), the construction and maintenance of basic public infrastructure such as train stations, public toilets, water storage tanks and disaster accommodation in rural areas are very difficult.
Forget rural areas, there are cities in which the lack of basic infrastructure affects millions of people every day. For example, Dhaka, the capital of Bangladesh, which houses over 20 million people, has fewer than 200 public toilets. People, especially women, life and visit, have to fight for basic amenities.
The 3D printing approach can increase the development of a significant public infrastructure in such places. Hopefully the success of the first 3D printed train station in Japan will serve as a practical and affordable model for countries that want to quickly improve their infrastructure.