GREELEY — Seven months into the largest Habitat housing project of her career, Cheri Witt-Brown can finally say her organization doesn't have to turn away families ready to buy a home.
Witt-Brown, executive director of Greeley-Weld Habitat for Humanity, has led Colorado's largest habitat project – Hope Springs. since the groundbreaking in June. By the time the project is completed, there will be 491 residential units, including 174 Habitat houses, and 320 apartments. Today, just over three months after work began, 27 fully constructed Habitat homes await families, eight more foundations have already been poured, and the first 3D printed duplex in Northern Colorado is almost ready for testing.
“In our 37-year history, we have never been in a situation where no one who qualified for a home had to be turned away,” Witt-Brown said.
SPONSORED CONTENT
Hope Springs is a collaborative effort by several organizations and individuals who have collectively raised $12 million to fund the Greeley Project, which will provide qualified low-income residents the opportunity to purchase a new home. The project includes single- and multi-family homes, hiking and biking trails, two mini-LED soccer fields, a community organic garden, a daycare center and a nature adventure park, all tucked away close to school, shopping and work.
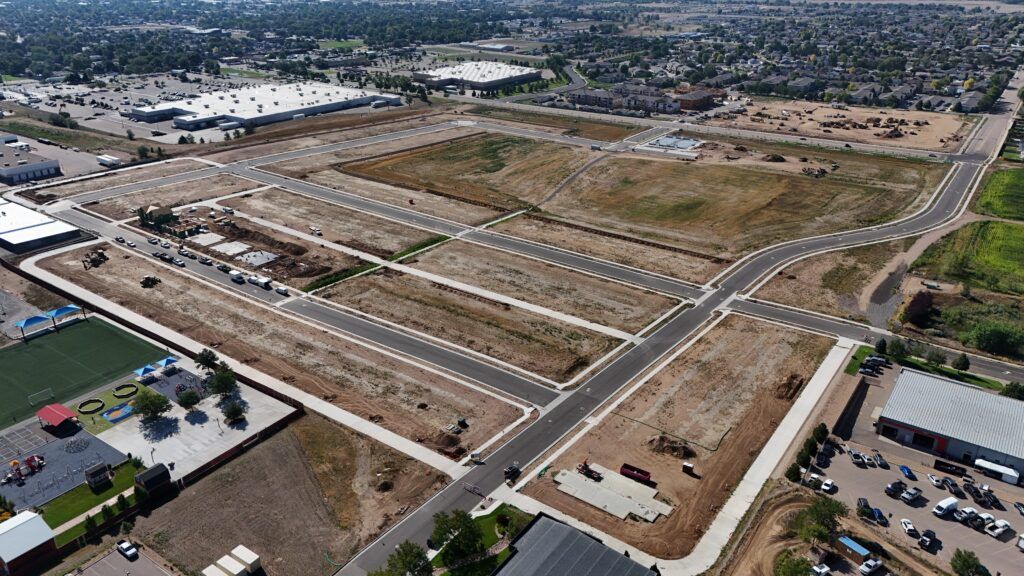
The focus of the project is energy-efficient housing construction. For this project, Habitat worked with Baessler Homes, which has built 27 homes for the project so far.
“With Baessler, we have a turnkey product and can house a family in a home from start to finish in 4½ to five months (including one month for loan paperwork and closing),” she said. “A Habitat home built with volunteers typically takes about six months. The end goal is to provide more families with well-built homes and quality construction. We can clearly achieve this goal with the Baessler product. Three and a half months is just an incredible production schedule. They have perfected a production model that is efficient without compromising quality and is difficult to achieve.”
In contrast, the pilot project to build the region's first 3D printed house took much longer. Alquist 3D, which received $2.85 million in state and local incentives to move its headquarters to Greeley earlier this year, championed the pilot housing project as a potential catalyst for building more 3D homes in Hope Springs. The company had already worked with Habitat in Virginia in 2021 and successfully completed three houses there. Although the company planned to build 200 homes, it pulled out of the project after initial construction, saying the project was too expensive for economic reasons, according to a report from WFXR TV in Virginia.
The technology and chemistry of 3D printing could still prove effective in Colorado's climate.
Before Alquist came to Greeley, a test project in Iowa failed in which the company planned to build ten 3D-printed houses in 2022, but only built one – it was demolished a year later because the concrete cracked under the stress of the colder environment , according to the Des Moines Register. That project also came with $3.2 million in state incentives, but much of that was for the educational component and Iowa State University's purchase of the 3D printer, the Register reported.
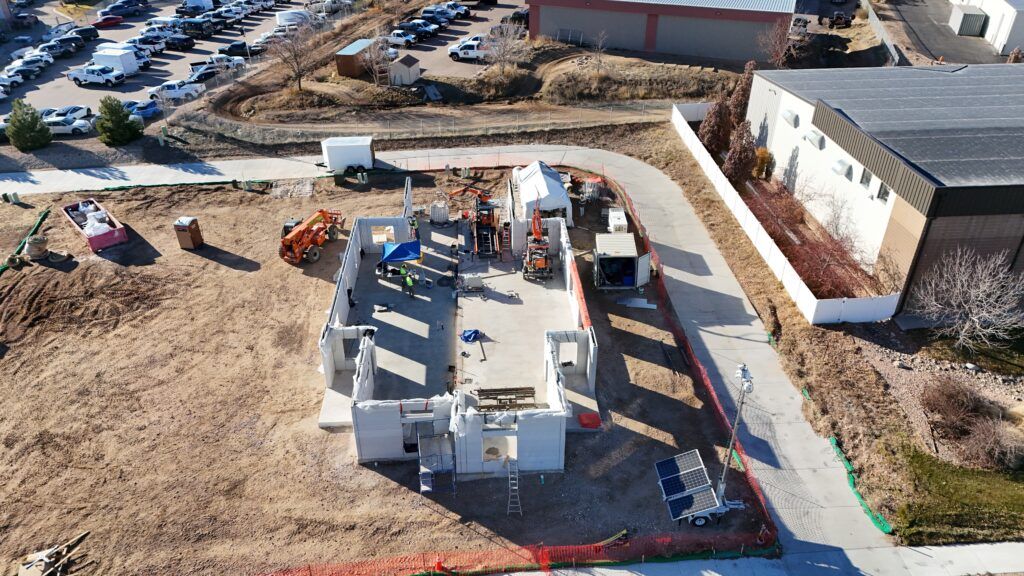
Witt-Brown said she and city officials witnessed Alquist's 3D work in Virginia, where Alquist built three 3D homes. This was spurred by reports of ICON's successful construction of 3D printed homes in collaboration with Lennar Homes in Austin, Texas. Alquist officials also recently built walls for Walmart in Athens, Tennessee, calling it the largest 3D printed structure in the world.
At a recent Greeley City Council meeting, Alquist CEO Patrick Callahan said the company is currently working on another Walmart. He said he understands and empathizes with the city and Habitat's frustration with the company wanting to quicken the pace.
“There's a collective disappointment that we didn't get faster,” Callahan said. “We are in the final stages, another frustrating issue, but we are very proud of the 3,000 square meter duplex, which is approximately 94% complete. In Tennessee the humidity was 100% and 95%. We had to learn to control the temperatures. …It’s different here. It is colder, so heating material was a process that no one in the world had mastered. We are the only company in the world to have built a duplex of this type, using a material that has never been pushed to these limits. It took longer.”
Witt-Brown said she believes in the technology but also wants to test it in Colorado's climate to see for herself. Now that the Greeley duplex is almost finished, she wants to put it through its paces – to make sure it's the best product that can be offered to any new family, from energy savings to the quality of life in such a home.
Witt-Brown originally intended a family to be the first residents of the pilot semi-detached house, in which Alquist only built the walls. As it turned out, the family chose a wooden house in which they could invest their own “sweat equity” to help build their home. This is Habitat's way of getting approval from their homeowners.
This first test of a 3D printed house, touted as being cheaper, quicker and cheaper to build, and more energy efficient, doesn't confirm that. The walls are expected to be completed this week, so Habitat crews can then build the rest of the project – framing, windows, roofing, as well as flooring and finishing.
Callahan told the city council: “The startup life is exciting; It can be difficult to have a lot of success and fail moving forward.”
So far, the cost savings from 3D home printing have not materialized. Habitat chose to build deeper foundations for the duplex with additional rebar and concrete to ensure the walls would be rock solid in the face of Colorado's strong winds or the possibility of a tornado. The walls replace traditional paneling and drywall. They had to add additional insulation to ensure the duplex could also retain heat.
“On both sides of the duplex, the additional cost for the foundation alone was approximately $40,000 per side, exceeding our traditional concrete,” Witt-Brown said. “Our costs today are 30-35% higher than traditional construction.” Callahan told the council that the work is their biggest challenge.
“Seventy percent of our costs are labor costs,” Callahan said. “We’re trying to attack the work side by using automated programming to reduce time on the ward.”
Witt-Brown has chosen to convert one side of the semi-detached house into housing for construction workers and convert the other into an office and show home where they can test for the next 18 months to find out how much more energy efficient the house is as well assess public interest, determine whether there is a market for the product, and test quality of life.
“We're not worried about the structure of the product, but one of the things we want to do is get feedback from the public: 'Do you like the aesthetics of this 3D printed house?'” One of the improvements Alquist is working on is their prints to make it more consistent. …It's almost like stucco, which will never be completely uniform, but we know it adds an extra layer of energy efficiency. These are all things we want to research and analyze and get feedback on.”
The presence of employees on site around the clock also helps to ensure the necessary security, as large construction projects are usually the target of theft. In recent years, Habitat teams lost all their tools on a construction project and had to start from scratch.
As part of the construction, Alquist must complete another phase of construction, namely printing and installing the gable wall section from the warehouse. Witt-Brown said she hopes the duplex will be fully completed in six weeks.
is LinkedIn