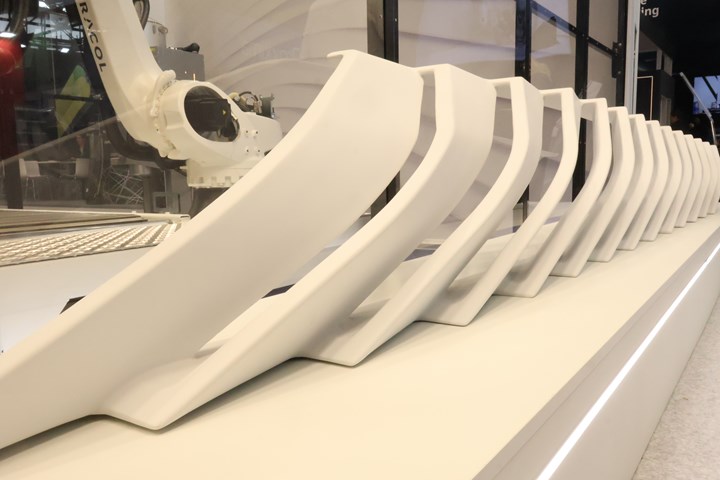
3D printed inlet grille. Source (all pictures) | Caracol
The GTX116 Sport Utility Yacht, which was produced by Pershing Yachten (Mondolfo, Italy), one of the seven brands of the Ferretti group, offers the way robot technologies for robot manufacturers of robot-large format additives (LFAM) enable efficient production of complex, super structural parts with exciting geometries. For this project, Caracol (Milano, Italy and Austin, Texas, USA) 3D print key elements were commissioned for the new range of yachts, including side air inlet grills and windshield spots.
Yacht air grilles and other buildings are traditionally generated by manual lamination of fiber on shapes. Depending on the complexity of the geometry, this process requires several forms and includes intensive manual work through highly qualified workers that influence the production time and costs.
In contrast, LFAM fully eliminates the need for Master shapes and tools, which optimizes the production process. Caracols Inclusion of the Heron on the system in this project – specializing in printing composites and polymers – achieved components with complicated geometries and highly adapted designs that could be produced directly from the digital model, whereby the manual lamination phase is bypassing. Caracol notes that this reduces prototype and production times and enables fast iterations and design optimizations. In addition, the process only requires grades such as gelcoat application, which means that labor-intensive steps will continue to take.
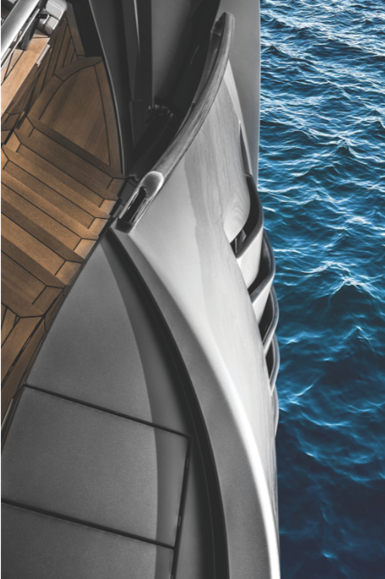
In addition to the use of light materials by Heron AM, its flexibility enables a small or completely tailor -made production that meets the specific requirements of each project.
The introduction of LFAM led to the production of air grilles with improvements in relation to efficiency, sustainability and general product quality. Caracol used his Heron 300 system, which was equipped with an extruder with high accuracy and a 3-millimeter nozzle. The components were made from ASA reinforcement with 20% glass fiber – a material selected for its durability and resistance to hard marine environments.
The 3D printing process took 72 hours, with an air cooler with a size of 4,200 × 400 millimeters and a weight of 40 kilograms. Compared to conventional manufacturing methods, this approach has led to significant reduction in the lead time (50%), material waste (60%) and total weight (15%).
In order to ensure both weather residues and flawless aesthetics, the radiator grille ended with a gelcoat, which improved its durability against environmental pollution.
The resulting 35-meter yacht yacht, which offers customers a sporty but elegant style, is expected to increase the sea experience.