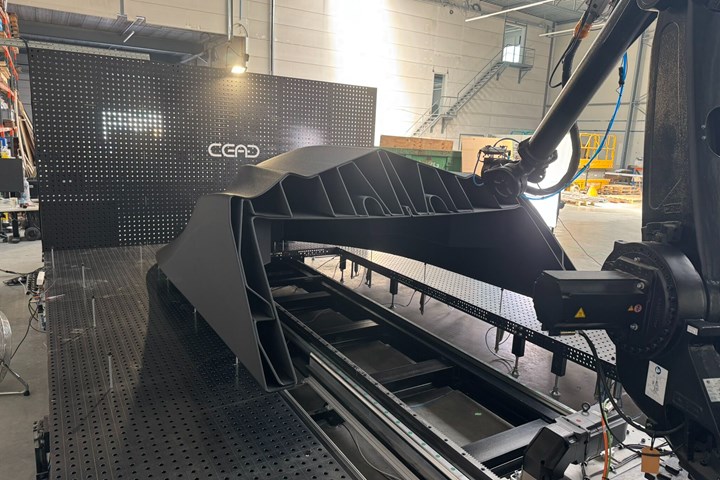
Fischerboot print on the Mac. Source (all pictures) | CEAD BV
The Maritime Application Center (Mac) started CEAD BV (Delft, Netherlands), an initiative that focuses on accelerating the introduction of the automated, sustainable production in the seabread. The Mac is positioned as an innovation center in which advanced production, material development and application technology are merged to combat the complexity of the boat building and the associated maritime components.
The Mac is a room of 2,300 square meters directly around the corner of the CEAD headquarters, in which boats are to be developed and manufactured by a highly automated, digitally powered manufacturing process. Mac starts the company's two -time vision for Marine. First, to provide production capacities to support shipbuilders and maritime manufacturers who are not yet willing to adopt large 3D prints in their own house, but strive to use the advantages of a highly automated production process. Second, in order to accelerate application development and thus take over the large-scale 3D printing technology in the maritime industry by closely sharing together with industrial partners and existing CEAD customers, developing solutions together and the limits exceed what is possible.
The MAC aims to demonstrate what the future boat factory looks like: a highly exhaustive, compact, automated facility in which only two to three operators can produce more than 100 boats a year, depending on the specific factory configuration. At Mac, CEAD is currently reducing production capacity to produce at least 100 boats a year, deliver the market and actively demonstrate technical feasibility, efficiency and proficiency of this factory model.
Overcoming traditional shipbuilding complexities overcome
Today the shipbuilter requires the combined efforts of an entire shipyard ecosystem, which is strongly based on qualified workers, large -scale infrastructures and complicated, interconnected value flows. Many shipyards have spent decades of optimizing costs and specialization and creating highly silent workflows and central resources. However, the latest demand growth is to burden the shipyards that are already retiring, aging the aging infrastructure and daily operational inefficiencies, which makes it difficult to quickly scale or adapt the market requirements. There is also an increasing demand to reduce the effects of maritime industry on greenhouse gas emissions, since the goals defined by the International Maritime Organization (IMO) demand that companies are transferring to more sustainable manufacturing approaches.
CEAD believes that the current conditions within the maritime sector are particularly suitable for a large 3D printing technology that deals with many of the bottlenecks that are currently exposed to the industry. For example, the large-scale 3D printing technology enables the production of boat fluffs directly from a digital file, which eliminates time-consuming, wasteful steps and the dependence on qualified manual workers is reduced. In this way it reduces the costs, shorten the lead times and enables manufacturers to quickly adapt to the changing market requirements for the design and production capacity.
CEAD has developed a dedicated system based on its extrusion technology, which was specially developed on automated 3D printing boat shelves. With this dedicated machine, the company has created production technology with which bootbuilding is possible in a way “not possible with standard robot -3d printers”. These machines form the basis of a production system with flexibility to scale production with increasing demand. In contrast to conventional shipyards, this boat factory works without the need for a strong infrastructure, zoning or workers, which makes it feasible in light industrial or even urban environments such as the city of Delft.
Innovation through partnerships
The Mac recognizes the complexity of the 3D printing of entire boats and is based on a collaborative model. Cead works closely with industrial partners and offers a platform for learning and growth. Partners can examine everything together, from 3D printing design for boat hulls to material development for sea environments to process optimization and software innovations.
The Mac is open to cooperation to shape the future of maritime production.
“We bring deep specialist knowledge in the large 3D printing technology, but real innovations occur when we combine this with the knowledge that our industry partners have: whether it is about boat design, regulatory requirements or real performance,” emphasizes Charléne van Wingerden, Chief Business Development Officer at Cead. “It is this exchange of experts that makes cooperation so powerful.”
Application focus: 3D printing industries
At the center of the activities of the Mac is a clear focus: development and refinement of the process of 3D printing for the professional maritime sector. It is currently aimed at boats up to 12 meters long and for industrial or defense applications such as work boats (patrol boats, fishing boats, supply boats, etc.) and unmanned surface ships (USVs). The team is involved with practical experiments and examines every aspect of the application.
The company recently introduced Cead HdPro, a new material that has exceeded conventional HDPE in high-performance maritime applications. These efforts led to the successful production of his first full fishing boat with CEAD HDPRO, which was completed in just 88 hours of printing time.
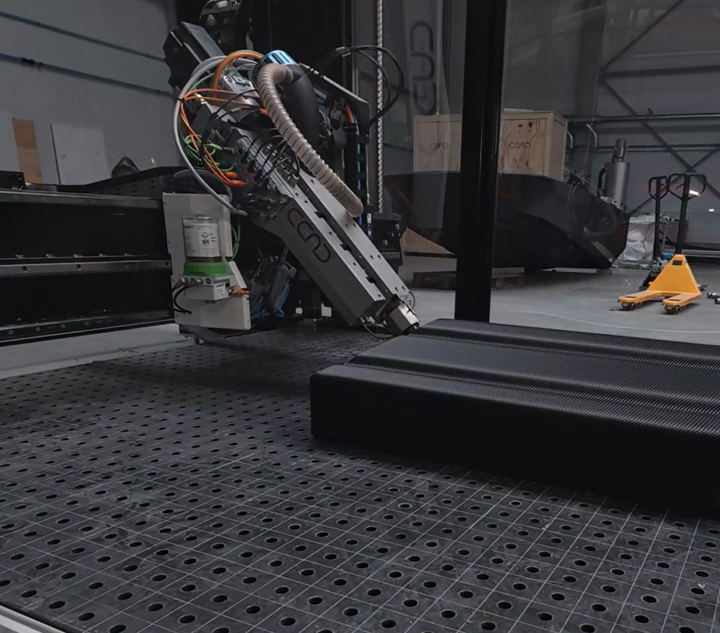
Fuel tank pressure.
“It is an exciting learning process. We learn by testing, optimizing and printing in real time. We have to find out new things, but that's exactly how real innovations are happening,” says Maarten Logtenberg, CTO at CTO. “The Mac is intended as a place for upbringing while you continue to learn and develop.”
Targeting of a future of local, automated and green production
Cooperation and innovation are important in order to achieve the goals defined by the IMO to reduce carbon emissions in maritime industry. The 3D printing technology on a large scale can handle the shipbuilders and operators to produce ships and components where they are needed and if they are needed. In addition, the Mac setup can be easily replicated in strategic places around the world, closer to the point of use in non -traditional, compact environments.
The Mac serves as a blueprint for an approach that CEAD refers to the “CEAD-powered microfactor”. These compact, compact and automated production systems are built up around CEADS technology, in which the machines are tailored to certain applications. Thanks to the modularity of the systems, this microfactor model is not limited to a sector, but is applicable in the industry. While the Mac was specially developed for maritime industry, other microfactories have already been realized, such as the recently introduced Haddy facility in Florida.