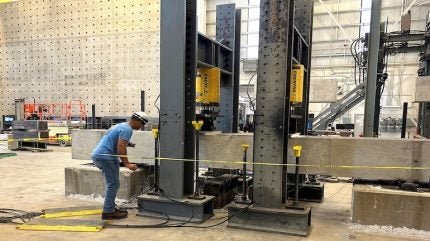
A nuclear of GE Hitachi (Geh) under the direction of a modular reinforced concrete composite material, which can significantly reduce the costs for the construction of nuclear reactor insulation structures. The rehearsals of the membrane plate steel network (DPSC) were tested in the Bowen Laboratory of the US Purdue University in Lafayette, Indiana. The new composite material is one of three advanced construction technologies that the US Ministry (DOE) examines by up to 10%to reduce core construction costs.
The DPSC design has several advantages over conventional composite techniques for reinforced concrete, e.g.
The steel wall modules can be produced in a shop and delivered to the construction site while the preparations are underway. The different modules are then compiled on site and filled with concrete, which leads to a faster assembly and installation reduction of labor costs and the project plan.
The modules can also be manufactured in such a way that they have different panel material on both sides of a wall in order to better meet certain corrosion requirements in nuclear power plants. During the installation, the modules can be welded together end-to-end or vertically in order to obtain improved design flexibility and faster quality control inspections.
The Purdue researchers filled the modular plates with concrete to simulate a reactor insulation wall, and suspended the structure of the different stress conditions to imitate real situations in which a reactor building could occur like an earthquake. Doe said that the little demonstration was a success and solved the way for the advanced building cooperative in future demonstration projects.
“The DPSC system tests at Purdue exceeded our expectations,” said Luke Voss, program manager at Idaho National Laboratory (InL). “We are very excited and enthusiastic about the use of this construction technology to save time and money when using new nuclear reactors.”
Sean Sexstone, Executive Vice President of Geh, Advanced Nuclear, stated: “The successful design, the production and testing of DPSC modules demonstrates the potential of this advanced manufacture and construction technology to lead to cost savings and improved project plans when using small, modular reactors.”
The data recorded during the small demonstration are used to support the licensing of the modules for use in the future reactor construction. The National Reactor Innovation Center (NRIC) from Doe is currently evaluating a proposal from Geh to create part of a reactor -containment building with the DPSC design for the Walling system in order to further test the technology.
The demonstration would also implement digital twin technologies for the civil structure and non-destructive assessment techniques that were developed in the original phase of the project. Go plan to use the DPSC technology for the first four units of the small modular reactor BWXR-300 for construction in Ontario, Canada.