Kris McCormack
;)
How do 3D printing and metal injection forms change that changes the golf club design? Learn the regulations, disadvantages and the future of these technologies.
Fairway Jockey
The production of Golf Club is not just about forging, casting and a man in an apron that grinds a wedge more by hand. The game continues to develop, as well as the tools.
Two of the most exciting technologies that change the golf clubs are 3D printing and metal injection molded parts (MIM) – and they are not just keywords. These are also not future ideas; They are already used by brands such as Cobra Golf to exceed the limits of design, precision and performance.
Let's take a closer look at what every technology is, how they work and why they bring golf equipment to the next level.
What is the 3D golf club print?
The 3D print in the Golf is a process in which club heads layer by layer from a digital file are created. For golf clubs, this usually includes ultra-fine metal powder (such as stainless steel or titanium), which are merged by a laser, which creates complex structures that simply cannot keep up with conventional manufacturing methods.
Cobra continued to pull this than everyone else in the industry … so far. Cobra not only prints components or internal structures; It is completely 3D prints of the entire head of your 3DP tour iron.
This includes the outer shell and the internal grille framework, all of which were created in a single build process. It is a brave step, but it opens up new opportunities in terms of weight savings and precision technology. Head designs like the 3DP tour would not be possible with traditional casting or forging.
3D positive:
– Design Freedom: Create shapes and internal geometries that cannot be done differently.
-Weight saving: Remove the mass from non-essential areas for better CG control.
– Faster prototyping: Engineers can optimize and test new ideas instead of months.
-Potential: one -time or player -specific clubs can be printed to complement a certain failure or a certain strike location on the face. (This is a really cool application.)
The fights:
-Legal production speed and less practical for highly volume parts.
– Higher costs, especially without the possibility of scaling production.
– Printed heads have to be ended more after production.
Cobras 3D printed iron pair Blade look with forgiveness of the season improvement
From:
Kris McCormack
What is metal injection form (MIM)?
Mim is like turning a golf club out of Metal Play-Doh. They take super fine metal powder, mix it with a folder to make it soft and formable, and then inject it into a form to get the desired shape. Then it goes into an oven in which the folder burns down and the metal merges together into a fixed piece. It is a simple oven for steroids.
What you have in the end is a clubhead that has the design of a shaped part, but the strength and the feeling of a fake. Cobra used this process for its royal skills, and the results speak for themselves – consistent forms, excellent feeling and beautifully clear lines.
Advantages of Mim:
– Territories: ideal for precision forms such as wedge grinders and sole geometries.
– Excellent feeling: an even grain structure leads to a softer, consistent strike.
-Efficiency with a high volume: ideal for the production of consistent heads on a scale.
– Refined surfaces: smooth surfaces and finer details directly outside the form.
Where Mim is missing:
– Tool costs: Forms are expensive and take time for development.
– Less design flexibility: Each change requires a new shape.
-Limited internal design: No possibility to meet the grid style of the 3D print.
Where could these technologies come from?
It gets interesting here. Both 3D printing and mim are just starting with Golf. Over the next five to ten years, we were able to see large breakthroughs in the way in which clubs are designed, built and even adapted for individual players.
Rocco convey tested Cobras DS-Adapt-Woods. We learned the following
From:
Johnny miracle
Full 3D printed club heads
We are not far from a world in which a driver or iron is printed as a single uniform structure – crown, face and internal support, all of which are tailored to optimize performance. This could unlock new sound moods, weight distribution and durability.
Think about it … You could have an adjustment and within a few weeks you have built a 1/1 set of iron or wedge for exactly what you need. Form, weight, loft, offset, all installed in the head designed for them. Um … yes, please.
Pressure waves, handles and hosels?
The 3D printing could expand into waves and handles with integrated flex zones, damping layers or ergonomic form. It could even enable multi-material construction within a single component.
Custom Player -Tuning
Mim's strength in volume and precision could lead to player -specific shapes: grinding, shaping and even weight distributions that are tailored to their swing profile. Combine this with AI-driven fittings, and you are looking for really tailor-made equipment for every level of skill or every weekly warrior with deep enough pockets.
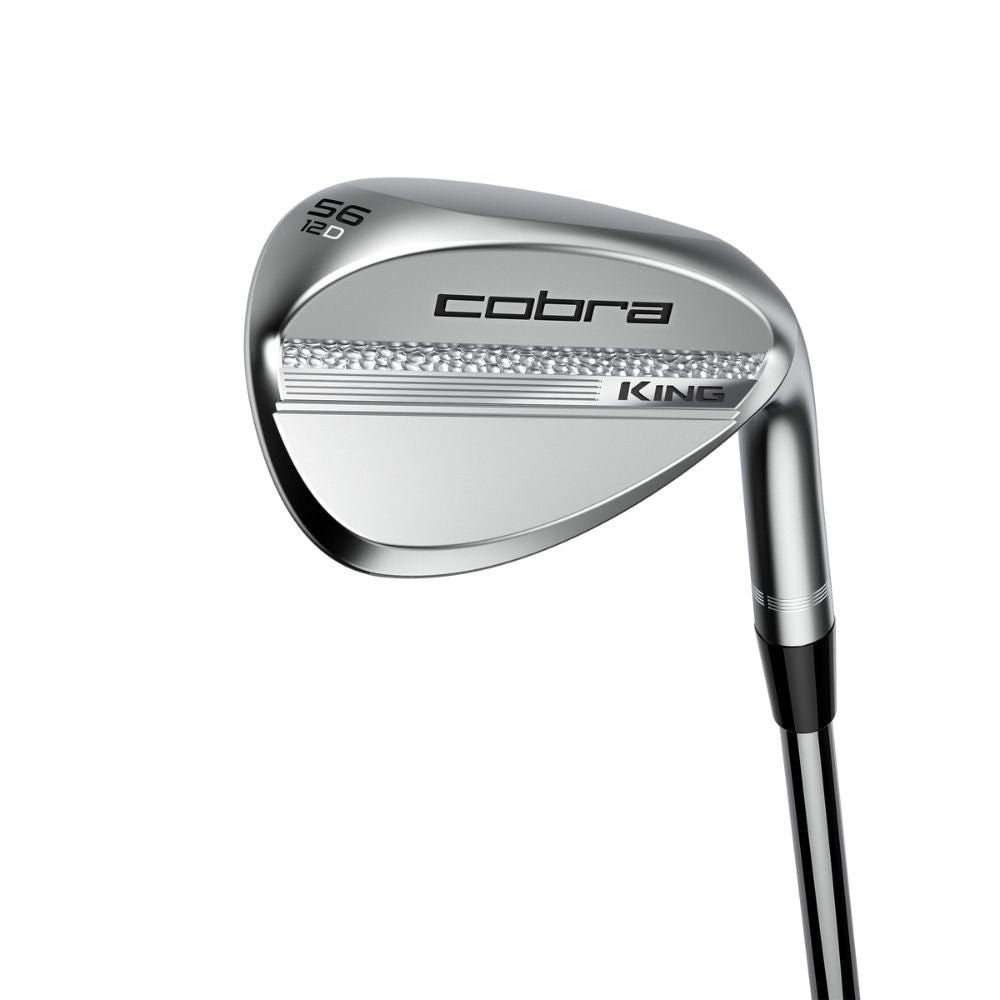
Cobra King Cendage Kedge
Royal skills made of 8620 steel with mim (metal injection form) are one of the softest feelings on the market. Choose from four new grinds (drop, widelow, versatile, tour) for improved Greenside creativity and optimized CG with Flight Window Technology (FWT) for the tour -inspired start. The newly designed Kobra speed guy, 67% larger than before, ensures better sliding and speed speed for shots with an open face. MIM (metal injection formation) Experience with MIM technology and offers 50% closer tolerances as conventional cast wedges. Each head is treated with heat at almost 1400 ° C, which ensures a closer grain structure for a softer feeling and improved longevity, which contradicts grooving for permanent performance. Cobra Speed Notch Discover the newly designed Cobra speed notch with a softer, mixed shape that complements our new loops. Now 67% larger, it ensures a smooth sliding through the floor, with retaining the speed and delivers high spinning.
View Product
Let's go one step further … Hybrid technology
Imagine a mimatic shell with a 3D printed internal core. One offers the precision shape and the feeling that the other gourmet performance from the inside out. This type of hybrid construction could become the new standard when building up the next generation of high-end club design.
Cool think about it, just not quite there.
3D printing and mim are not here to replace forging and casting. You are here to add the toolbox. Both open the door for new possibilities for club designers and engineers. And while brands like Cobra lead the fee today, the Ripple effect could change the entire equipment landscape in the next decade. Just take a look at what laboratory did with the putter design.
Are you ready to update your bag to the latest technology? Book your next adaptation in your local actual specification.
;)
Kris McCormack
Golf.com participants
McCormack built up on a career that has exceeded more than 20 years in the golf industry, and spent the last six years of his career as a vice president for tour and education for real specification golf. During this time he curated the training program for the real SPEC -matching staff and urged himself to the curriculum for further training. As well as the management of your travel department and build -up relationships with a variety of OEM partners. Before McCormack entered the true specification team, he worked with several industry-leading manufacturers as a master specialist. In addition to the instructor and partnership with the Golf Channel Academy as the main trainer and brand -independent specialist. He also worked with F&E teams to support product design, tests and the development of a large number of equipment. He is a golf enthusiast and lives in the equipment room!