Robots, the cement walls for layer, have built houses in Houston, apartment blocks in Germany and a train station in Japan.
Now the 3D print two of the most famous retail companies in the world, Starbucks and Walmart, has failed, who have debut both 3D printed facilities in large fanfare in the past few months.
Technology supporters say that it is faster and cheaper than conventional construction methods. And with a large buy-in in retail, the 3D-printed building has officially become mainstream.
However, this does not make it an intelligent bet for most commercial real estate developers.
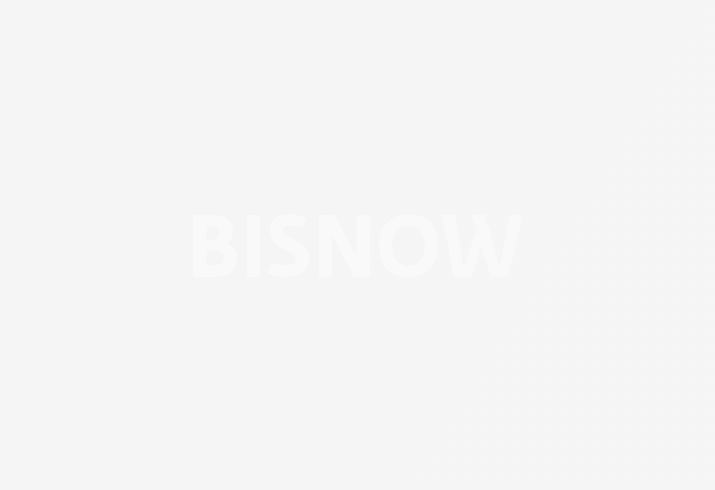
With the kind permission of RIC Robotics
Equipment from Ric Robotics 3D print the walls of a building made of cement.
In the past few weeks, top-class projects have multiplied in 3D printing.
Walmart used a 3D printing system from RIC Robotics last year to build the walls in two new facilities in Alabama and Tennessee.
Starbucks has entered Peri 3D Construction for the construction of a shop closed in Brownsville, Texas.
“For the first time we don't talk about the 'potential' of the 3D printing – We have achieved real savings in time and work, ”said RIC founder Ziyou Xu about the Walmart projects.
Few do not agree that the technology has potential. Whether the era of the 3D cement printed with mass production is printed is for the debate, with some are openly concerned in the field, that it is checked and the public turns on if they cannot be submitted.
“People exceed this technology and the media buy them,” said Lucio Soibelerman, professor of the University of Southern California.
“I want you to be more transparent with people,” said Penn State Professor Ali Memari, who completes the school Pennsylvania Housing Research Center. “We don't want to create too much expectations … it can damage the industry in the future.”
“Box Building”
XU sees the technology as a solution for the stark lack of work in the US building industry. This year the nation has to move 439,000 new employees into the sector to keep up with demand.
“Young people don't want to get cement all day, but they want to play with a huge robot,” said Xu.
The founder of RIC Robotics has been working on 3D printing technology since his student at Tsinghua University in China in China 2016. He then went to Columbia University to make a master's degree in architecture, but in 2021 to found the company.
RIC's 3D printing technology has made great progress in recent months, said XU.
His work on the first Walmart project – An 8K SF supplement in Athens, Tennessee, completed in cooperation with Alquist 3D – Required 30 workers and lasted 45 days.
“The structural design was not as optimized as it could be,” said Xu. “There was a big learning curve.”
The next Walmart project from RIC, the 5 -km -sf warehouse in Alabama, required only five workers who completed the project in seven days, including equipment. It delivered two weeks before the schedule in February.
Xu rejected it to share a construction price for the Walmart projects, but told it Bisnow The 3D printing systems from RIC mounted on RICS can be rented for around $ 9,000 per month.
“They basically build,” said Memari. “It's just a huge concrete box and then the roofs are trusses.”
There the skepticism creeps in.
According to Soilman, Walls only make up about 20% of the costs of a new building. The rest of the project, including the roof and other surfaces, must be carried out by workers.
“It is what I would describe semi -automatic,” said Memari. “The rest of the construction is traditional.”
Installing reinforcement rods gives the process another complexity level. The pressure must be carried out so that the workers can place it by hand.
“You have to drop the reinforcement rod into some cells and fill them with mortar,” said Memari.
Most 3D printers cannot work. Without the total volume, the budget for a project can quickly take off.
“Cement is more expensive than wood,” said Soilerman, who has been added that the 3D-printed building is not very green.
“Cement is one of the most sustainable materials,” he said.
An answer to the real estate crisis?
Booster of the 3D cement pressure believe that they can make the most difference in the living sector.
“I consider this in response to the real estate crisis,” said Kevin Paul, Senior Vice President of H2M, who has teamed up with SQ4D, to build a 3D-printed house on Long Island around 2021.
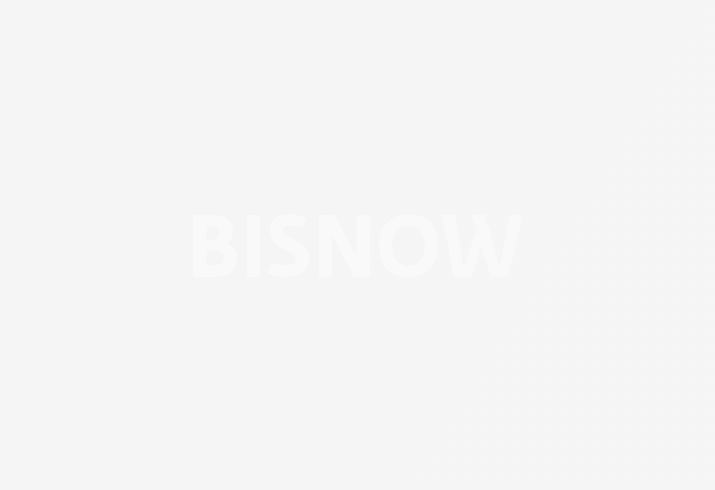
With the kind permission of RIC Robotics
A Walmart Store Extension Ric Robotics equipment has built up in Athens, Tennessee.
The budget of H2M for work and material was between 30% and 40% lower than what it would have been to build a traditional, spiked house at that time, said Paul. The number does not contain the costs of 3D pressure equipment.
This is a great effort, but it can be compensated for if the same equipment room is used to print dozens of houses in a standardized, levittown suburb, said Paul.
But it doesn't play that far.
Icon Build is a company in Texas that has made a name for itself for 3D printing cement houses and has completed the last of 100 such houses on the Wolfs Ranch near Austin last summer.
Instead of building inexpensive houses for the working class, it has highlighted the cool factor.
“You don't really sell it as an inexpensive solution,” said Soibelerman. “You sell it as a science fiction solution for people who want to buy something cool.”
The houses printed by icon and similar companies do not resemble the traditional suburb of the bungalows that many buyers are looking for, some say. Buyers should not expect crown strips or other custom details that are easy to meet through the traditional construction process.
“Customers have to shop,” said Paul. “If you tell people that they only have limited surfaces, they have to be on board somehow.”
A lack of adaptation has also been disadvantageous for the modular living space, another praised form of construction technology, which, as expected, never completely decreased, said Memari.
“People like special houses,” he said. “The conventional home industry has a lot of flexibility.”
However, if 3D printed structures can be built up in a tight budget on a scale, Paul believes that they could address the right demographic population.
“If you look at someone who lives in a apartment in Brooklyn in a apartment in Brookly, mostly very happy, with a concrete house with three bedrooms with a decent kitchen and two beautiful bathrooms,” he said. “Will customers see Hamptons the 3D printing? Absolutely not.”
Texas has more relaxed building regulations than the north-east markets Paulus generally works, which makes it easier to build 3D printed structures.
But also there Icon installs the insulation in his houses. For this purpose, Soilerman said that the company prints two separate walls and places an insulating foam between them.
“It's twice as high as work, double materials,” said the professor.
Niche applications
From the construction of the construction, cement cannot be sustainable, but offers some important advantages in a world that struggles with climate change.
Paul sees 3D printed houses as better for flood-prone areas than stick framework structures, since cement can rotten or wash away less often than wood. In some cases, evacuated could return after a storm and simply rinse their houses with a garden hose.
Concrete is also more heat -resistant than many other materials, which makes it well -at -fire markets like Los Angeles. The working nature of 3D printing means that it could be implemented there as a homeowner, said Soilman.
“I'm not against the technology,” he said.
Traditional forms are already doing when it comes to creating complex curves from concrete, said the professor. He is also happy about tire printing technologies with which cement can be printed without cumbersome rail systems.
Memari believes that the technology is also well suited for tiny house construction.
Most of the buildings in the USA are too big to have a 3D printed roof, but that is not the case for tiny houses, said the professor.
Cement roofs cannot maintain their structure if they rise in the same mild angle as traditional roofs, which means that they should be exceptionally large if they come to a point at the top. But tiny houses can absorb the steeper angle in a manageable height.
Memari and Soibelerman agree that the expectations of the public must correspond to what the technology can actually deliver.
“We have to do more research,” said Soibelerman.