The strength and structural integrity of concrete are not only due to its material properties, but also in the way it is shaped during the construction. An architectural student has developed a clever way to build strong, stable vaulted bonds with far less concrete and steel steel than usual.
The developed form of Lotte Sender Bieschin, a doctoral student in Switzerland in ETH Zurich, is a reusable frame for the shape of wet concrete until it hardens in its final form in arched soils.
Using a sophisticated structural geometry, they form vaulted bonds with 60% less concrete and 90% less steel compared to conventional methods. This can significantly reduce carbon emissions and the material waste associated with the construction work, especially in view of the fact that concrete production contributes to so many 7-8% of CO2 emissions worldwide.
ETH News: Form of development
A curved soil has a curved, arch -like profile and is typically stronger than flat plate floors because it uses compression to resist loads. However, such structures can require more complex formwork to create the curved shape, and often special skills to carry out properly.
This is where the form of development comes into play. Schlaus-Bieschins formwork uses stripes made of plywood and textile hinges to form and shape concrete vaults. The formwork itself is easy, easy to unpack, can be reused and does not require any petroleum -based materials such as styrofoam. This makes the design a more sustainable choice in addition to the material savings.
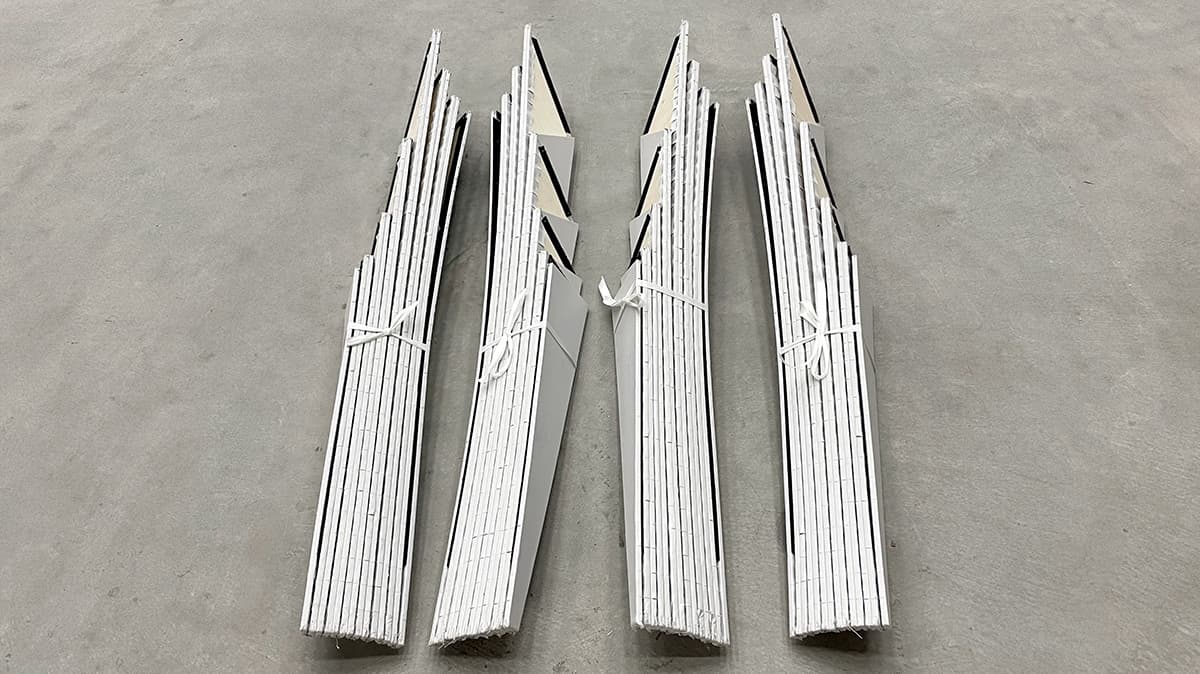
Andrei Jipa
This formwork of flexible plywood strips can be unfolded like a fan. Four of them can be assembled in a wooden frame to create a robust shape to which concrete can be watered directly. The zigzag form enables the formwork, which weigh only 52 LB (24 kg) -to support 1 ton of concrete and can be removed under the concrete reused from the hardened concrete.

Andrei Jipa
Timer-showed bieshine applied her understanding of bending structures, in which the deformation of elastic materials creates stability without weighting weight to design the formwork. The zigzag pattern that she developed for the plywood strips strengthens both the shape and the concrete that it supports. Your approach also includes an origami-inspired technology, which is referred to as wrinkles with curved distribution in order to obtain increased rigidness in the formwork.
“The developed form formwork can be manufactured and compiled without specialized knowledge or high-tech devices,” said Scheder-Bieschin. “The only things that are required in addition to the materials are a template for the shape and a staple.”
This makes it a practical option for construction projects in developing countries that have to set up buildings quickly and cheaply.
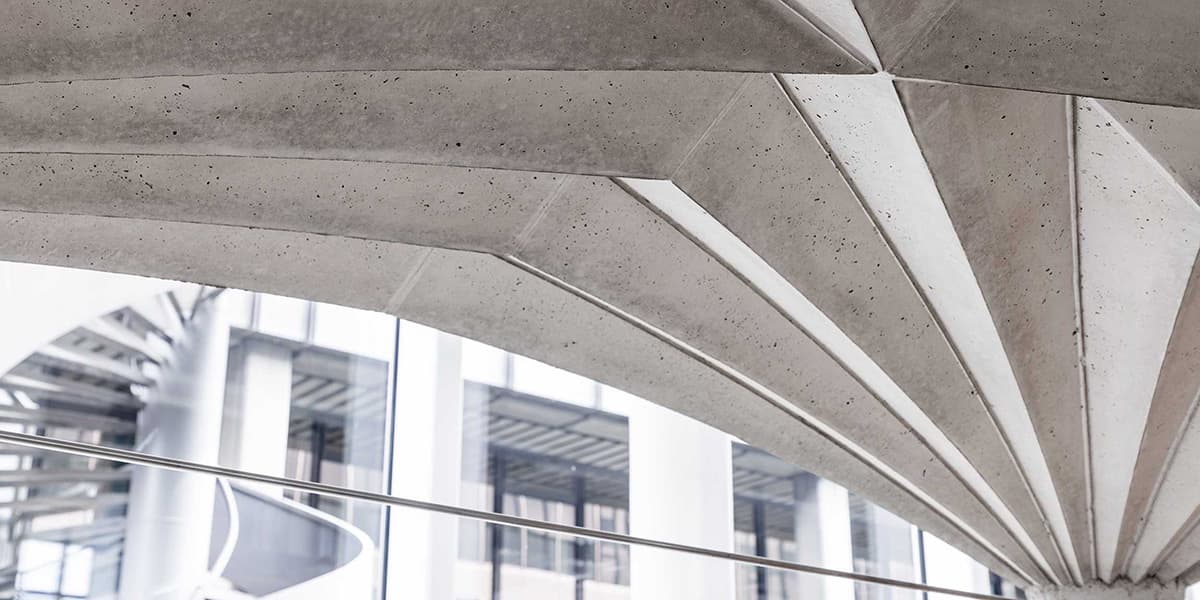
Andrei Jipa
So far, two concrete structures have been built: a 3.8-f floor of 9.8 feet 3.8 m (9.8 feet) on the Hönggerberg campus of ETH Zurich and its twin in Cape Town, South Africa, 3 MX 1, 8 m (1.8 m). The latter used organic conconcents with crushed invasive vegetation from the area. This has a sustainable construction company that does not take confidence in the trust of the innovative formwork systems in order to build high-quality, worthy and sustainable apartments in South African townships, “said appointments.
As soon as she finished her doctorate, Scheder-Bieschin will strive to commercialize the developed form and to design a market hall with her system in Cape Town. Such projects as well as others like this concept for hollow bricks, which are surprisingly difficult, can help reduce the amount of concrete that we use, and the massive greenhouse gas emissions to which you contribute to making a dent worldwide.
Source: ETH Zurich